Piece by Piece: Overhead Cranes Explained – Part 4 – Cabs
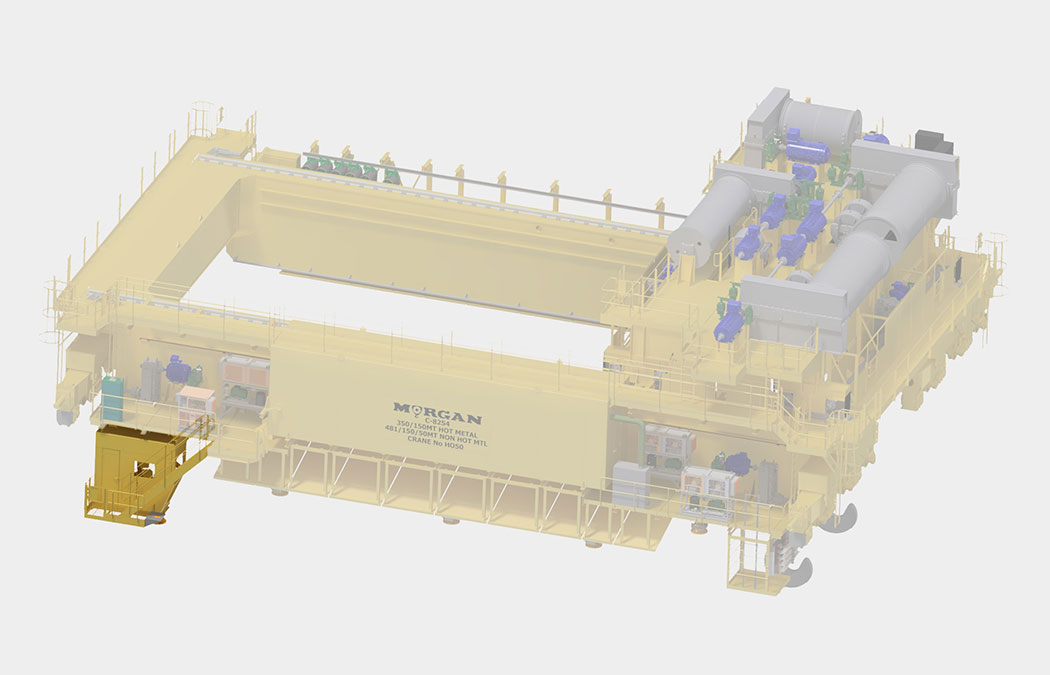
/ Blog
At Morgan Engineering, our expertise in manufacturing overhead bridge cranes extends to every component, including the crane cab. Our overhead cranes are designed to last, made up of several critical parts: trolley, bridge, cab, and control house. In this installment of the Piece by Piece series, we will focus on the intricacies of the crane cab.
If you haven’t already, review our previous parts of Overhead Cranes Explained for a comprehensive understanding of overhead crane parts.
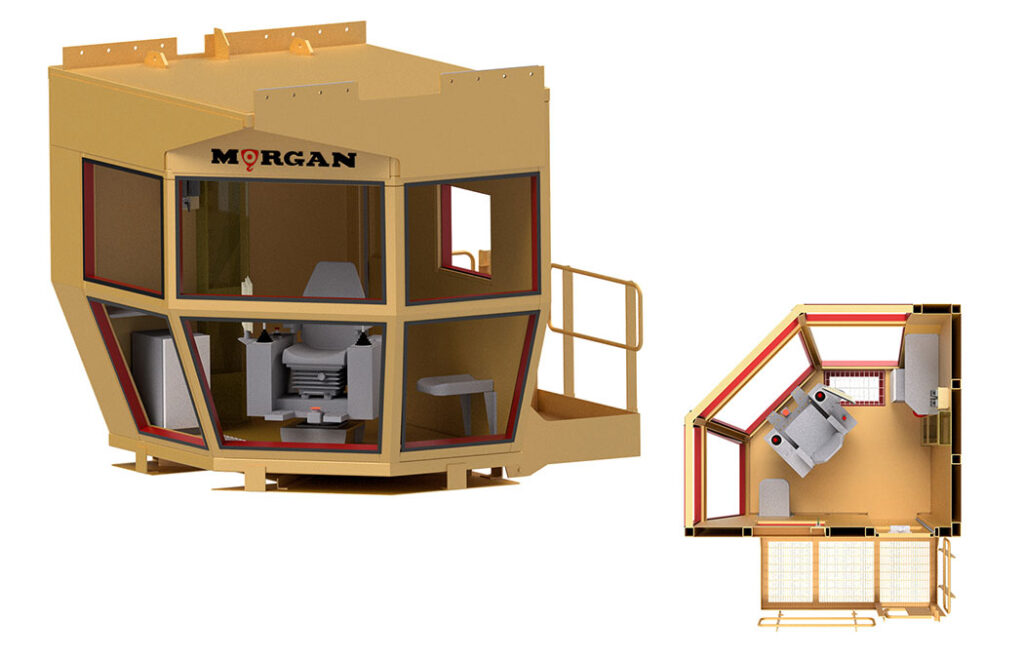
Front-view and above-view of a 3D-model of a cab.
A Crane Cab Defined
The cab on an overhead crane is more than just a component; it’s the operator’s command center. Crane cabs are commonly utilized in high-production environments for an elevated vantage point. A cab is typically located on the bridge or trolley but can be remotely mounted as well. If the crane is used on a more part-time basis, operators may use a radio control system on the ground to operate the overhead crane.
The main components of a crane cab are:
- Cab structure
- Glass
- HVAC
- Operator’s Chair
- Plant Radio Systems
- Human Machine Interfaces (HMIs)
- Cameras
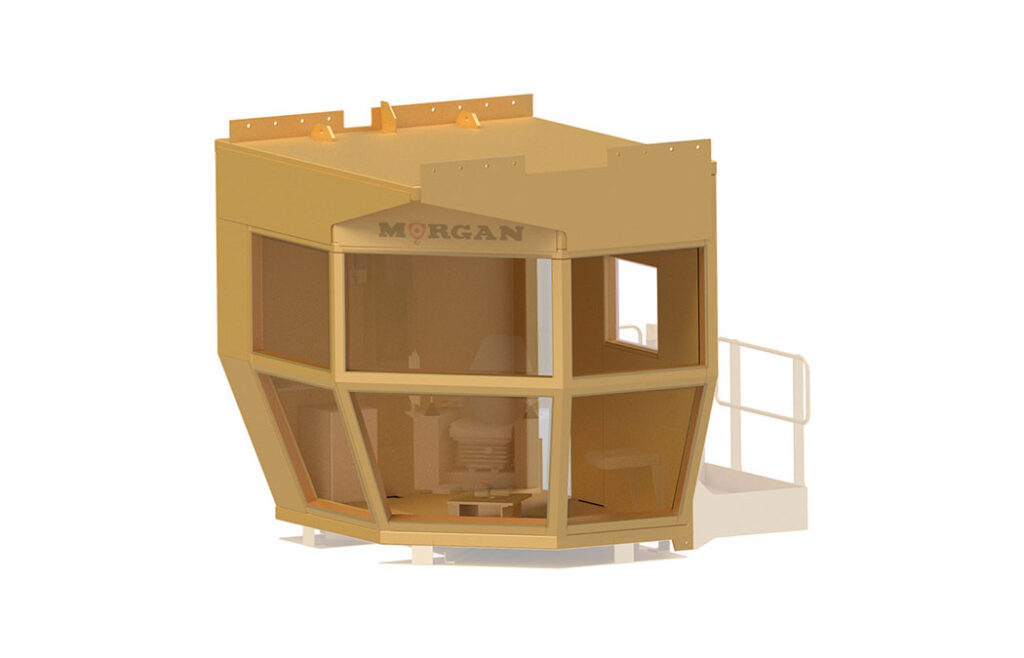
The cab structure of a cab is the metal frame in which all components are housed.
The Cab Structure
In an overhead crane cab, the structure is meticulously crafted to offer the best vantage point for the operator. The size and design of the frame is tailored to meet specific needs, considering comfort, visibility, and environmental factors like noise reduction and temperature control. Once the framing is placed for structural loads, glass opening allowances, doorways, and wireways; the remaining areas are metal skinned inside and out with insulation between for heating and cooling as well as noise reduction.
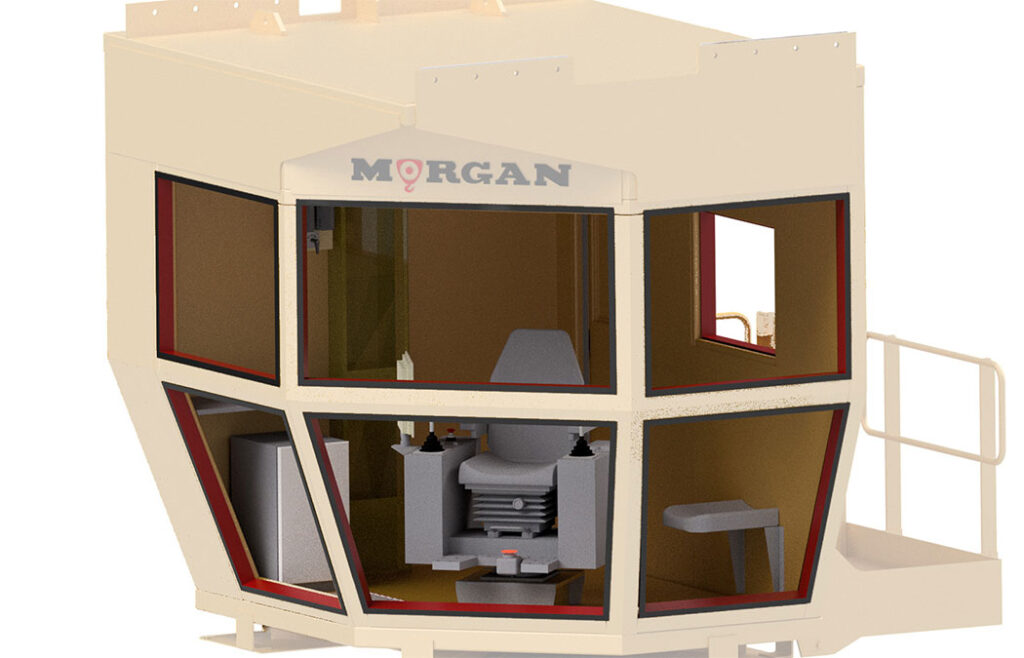
It is necessary to have glass designed to withstand harsh conditions on the cabs of cranes in environments such as a melt shop.
The Glass on Crane Cabs
Visibility is critical when operating an overhead crane. Glass commonly covers at least three of the four walls of a crane’s cab to provide the operator maximum sightlines.
Additionally, glass walls on a crane cab provide protection. The thickness begins at a quarter inch thick with an air gap between two panes and the second glass layer can increase from there based on the environment a crane will be in. For example, glass on a cab in a melt shop needs to withstand explosions and much higher temperatures than a lightweight crane running for general use in a balanced environment.
When extreme heat is present, the double-pane glass will have the same look, but the second pane will be a heat shield for extra security. It can have added coatings for IR, anti-glare, and tinting as needed for specialty applications.
Along with insulating the structure for temperature control, it can also significantly dampen sounds. This protects the hearing health of the operator.
Based on requests from customers we can design the glass to tilt, be replaceable, or slide for cleaning needs.
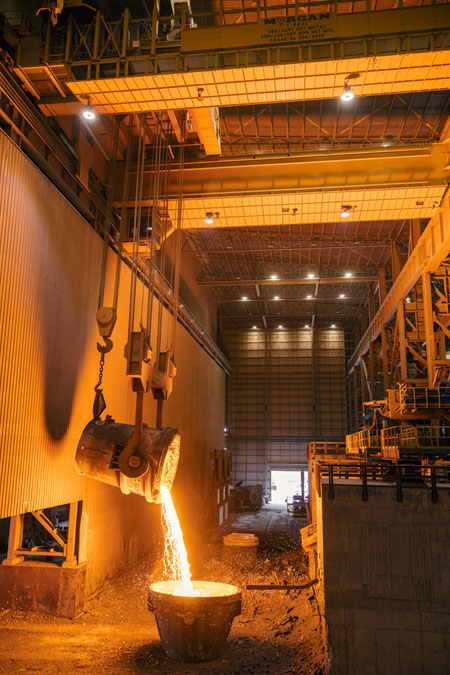
A temperature-controlled and clean cab is necessary to help protect against operator fatigue.
HVAC Systems in Overhead Crane Cabs
The HVAC system in an overhead crane’s cab plays a dual role in ensuring temperature control and air quality. Depending on the crane’s operational environment, the cab might include air conditioning, heating, and filtration systems: all crucial for maintaining an optimal work environment.
Multiples of these systems can also be supplied as well if the crane’s operation is critical or if there are safety concerns in the event of failure of one of these systems.
It is important for the crane operator to be in a healthy environment while operating a crane to limit distractions and reduce operator fatigue during his/her shift.
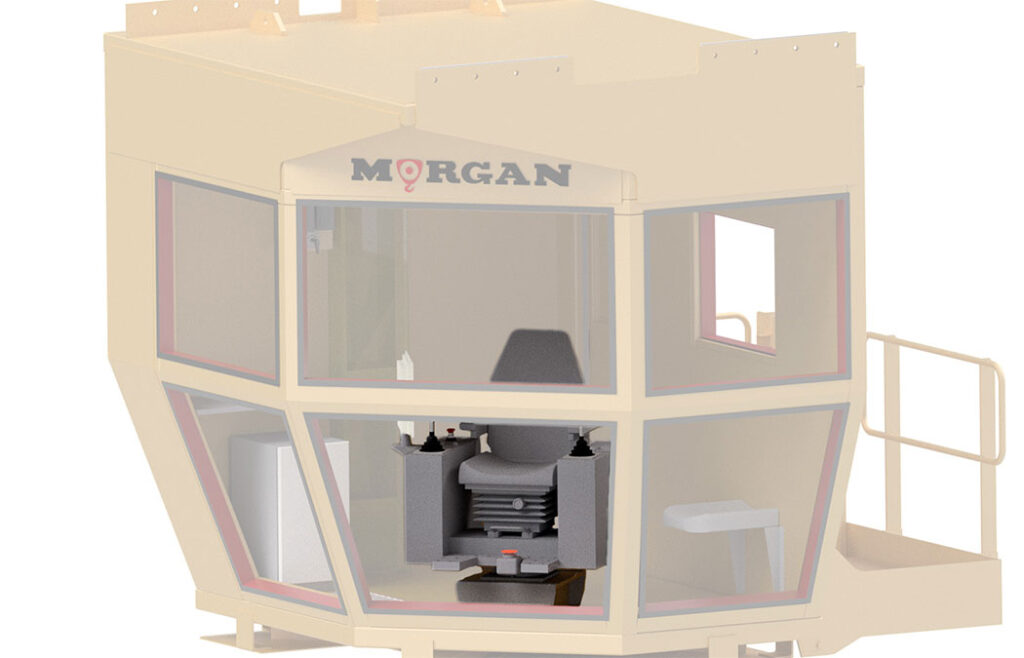
A comfortable operator chair allows operators to have greater control over the crane they are operating.
The Operator’s Chair
The importance of a comfortable operator’s chair cannot be overlooked. The operator is expected to spend the entire shift in this chair. Operator chairs are specifically designed with comfort in mind and are aimed at reducing fatigue. Conveniently located controls ensure all functions of the overhead bridge crane are within comfortable reach of the operator. Chairs can also be equipped with pneumatic suspension as well as heated seats.
Morgan works with numerous chair vendors to provide the best possible solution for the customer. Using the latest in 3-D modeling technology, we can give our customers an accurate line of site model for optimal cab/chair location on the crane.
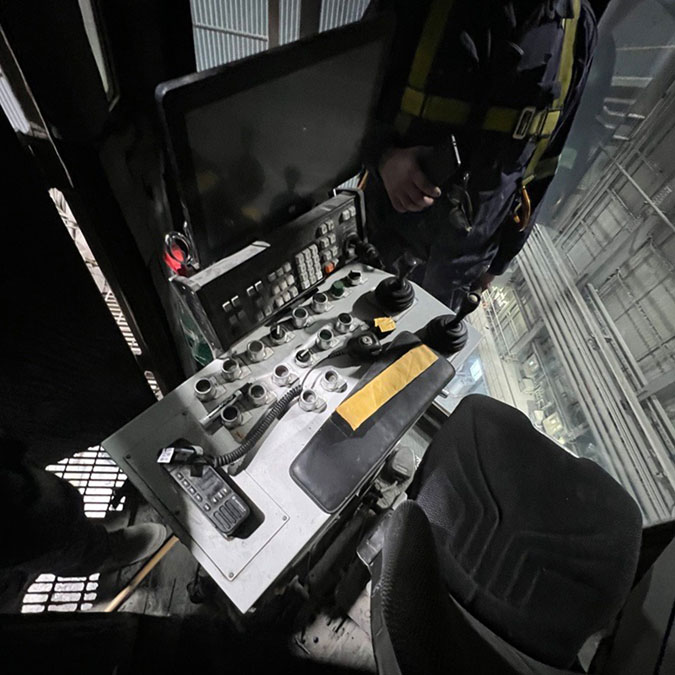
Example of a plant radio system.
Plant Radio Systems
Solid communication between the overhead crane operator and the ground crew is vital for seamless production. Any changes in plans, questions, or updates can easily be shared through these radios. They work similarly to walkie-talkies where anyone who has a corresponding radio can hear and respond to a message. These systems can be incorporated directly into the operator’s chairs so that they are always within reach.
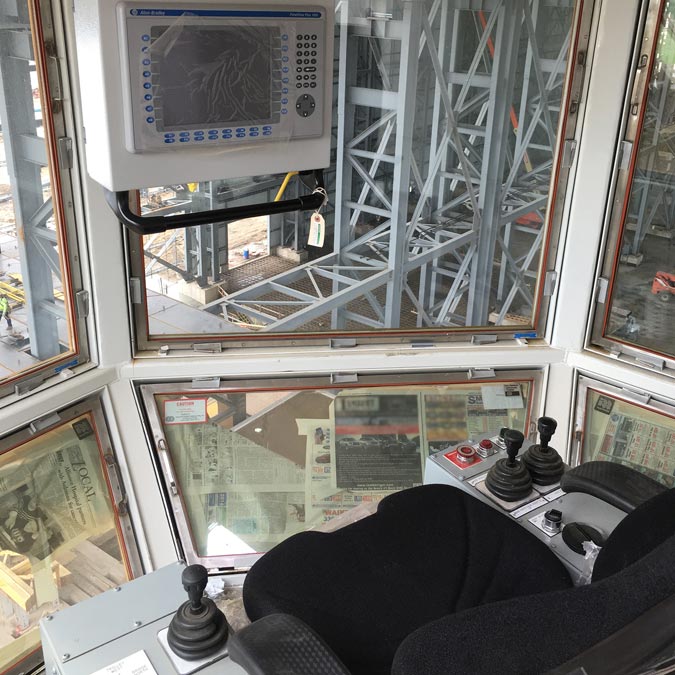
The view from inside a Morgan cab.
Human Machine Interfaces (HMI’s)
Human machine interfaces (HMI’s) in overhead crane cabs help to connect the crane operator to the crane itself or the mill itself. Screens are typically placed in the operator’s cab so that the operator can keep tabs on the crane’s performance and the mill’s production. The HMI’s can be mounted on arms connected to the wall or even mounted on the chair for easy viewing.
Morgans Crane Management System allows an operator to monitor the overhead crane functions and report issues about the maintenance should anything arise. It will also allow the operator to maintain/modify settings for the crane cab’s HVAC systems.
Customers can also add additional screens in the cabs that will allow the overhead crane operator to keep track of the mill’s production and help to give them a forward look at where material will need to be moved.
Cameras for Crane Visibility
Cameras are integral to modern crane cabs, eliminating blind spots in a cab’s visibility and enhancing overall safety. Cameras can be strategically located around the overhead bridge crane with the feed directed back into the cab and displayed on a TV. With additional engineering and hardware, mill cameras that are not located on the crane can also be displayed in the cab as well. This may include cameras located near a scrap pit or a preheater. In these scenarios, it is difficult for the operator to see the crane’s hook and ensure proper engagement in the item they are attempting to pick up.
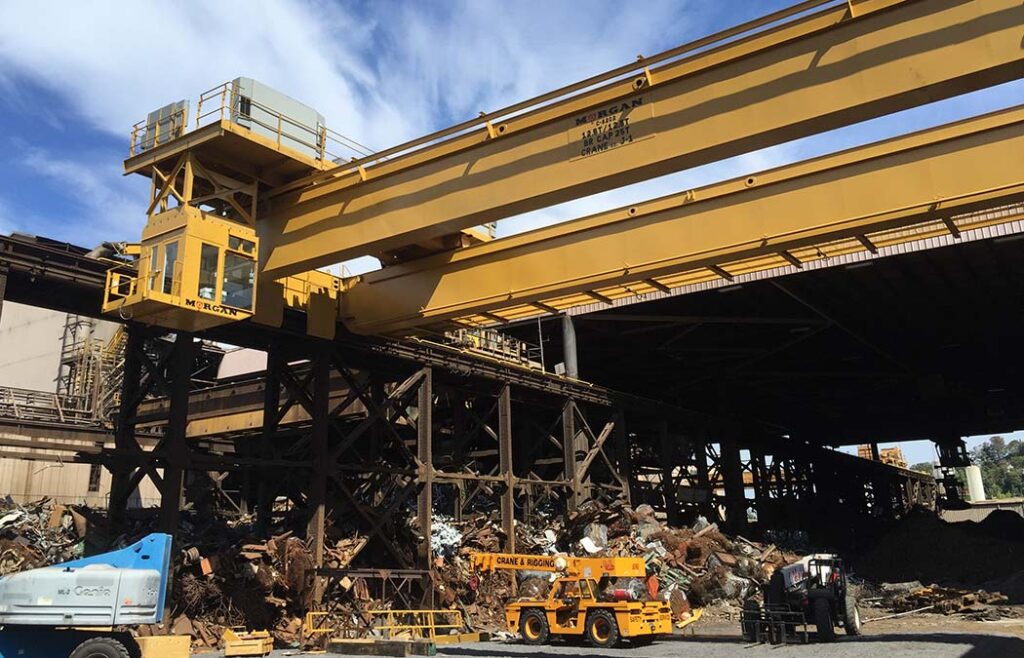
A newly installed Morgan scrap crane, the cab can be seen on the lefthand side.
How a Cab is Designed
Crane cabs are very carefully engineered because they hold a human life. At Morgan, safety is always our first priority. It is vital that we have the customer’s needs and wants outlined before beginning on a new crane cab.
The design of overhead cranes’ cabs overall is fairly standard. The changes are based on comfort levels of the operator and the function of the crane. It is very helpful for us to have an open dialogue with an operator who is knowledgeable about the bay the overhead crane will run in. This gives an idea of where the cab should be positioned on the crane as well as where the operator will be boarding.
We work to be flexible with a customer’s requirements so each cab we create is safe and custom.
Customize a Crane for Your Company
From the structure to the intricate components like glass, HVAC, and HMIs, every element of a crane cab is crucial. Stay tuned for future installments in our Overhead Cranes Explained series by following Morgan Engineering on Facebook, LinkedIn, X (formerly Twitter), YouTube, and Instagram.
Elevate your overhead crane to new heights today. Contact our expert engineers to see how we can create a custom crane solution that fits all your company’s needs.